Il ne s'agit pas de faire ici un
cours sur la résistance des matériaux mais seulement d'exposer quelques notions
élémentaires pour en comprendre un minimum.
Tout d'abord, il faut savoir que la
déformation d'un objet implique que la distance de certains couples de points de
cet objet varie. Ceci est une propriété géométrique (négation d'une isométrie).
D'une façon plus simple on dira qu'une partie de cet objet subit une compression
et une autre partie un étirement
Un exemple d'école est celui d'une
poutre à section rectangulaire qui subit une charge
Au départ ABCD est un rectangle donc AB
=CD
Sur ce dessin on constate que sous
l'effet de la charge matérialisée par la flèche la poutre qui repose en D et C
subit une déformation qui entraine une diminution de la distance AB et une
augmentation de CD
La fibre AB ou plutôt la couche en
surface AB subit une compression et la couche du dessous DC subit un
étirement
(On a fait l'hypothèse de conserver
des angles droits en A,B,C,D )
Les couches internes subissent
égalent des compressions ou des étirements mais leur amplitude est moindre que
celle des couches de surface.
Il existe au milieu une couche qui
n'est ni comprimée, ni étirée. Elle est appelée couche (ou fibre) neutre. Elle
sépare la partie comprimée de la partie étirée
On constate donc que la rigidité
d'un objet est liée à la capacité du matériau à s'étirer et à se comprimer.
De plus la forme géométrique influe
fortement sur la rigidité de l'objet. En effet, pour un même affaissement de la
poutre (flèche) la différence des longueurs de l'arc AB et de l'arc CD est
d'autant plus grande que l'épaisseur (AD) de la poutre est importante. Ainsi la
forme géométrique peut être telle qu'une petite déformation entraine localement
de gros étirements ( ou compressions)
Ceux qui ont une certaine
expérience de la construction plastique des canoës ou des kayaks savent bien
qu'il faut avoir une plus grande épaisseur (ou même des renforts de rigidité)
sur les grandes surfaces planes, que sur les surfaces fortement incurvées
Remarque: Dans la construction dite
"sandwich", on utilise pleinement ceci en essayant d'augmenter fortement
l'épaisseur AD en remplaçant les couches internes (qui travaillent très peu
pendant une flexion) par un matériau léger
Une petite expérience à faire:
1) Si vous prener une feuille de
papier vous constater qu'elle n'est pratiquement pas élastique et poutant elle
n'a aucune rigidité. Ceci est du à sa très faible épaisseur
2) Si vous prener une plaque
caoutchouc elle ne sera pas rigide bien qu'épaisse car il s'agit d'un matériau
très élastique
(faites un dessin sur les deux
faces et vous verrez mieux comment une face s'étire et l'autre se compresse)
3) Si vous coller sur les
deux faces de la plaque en caoutchouc une feuille de papier vous aurez un
ensemble relativement rigide (ne pas utiliser un papier trop fin qui risque de
se froisser).
Si l'épaisseur de notre poutre, mis
sous flexion, est très importante la déformation sera alors quelque peu
différente du cas précédent. Le dessin ci-dessous illustre la
situation
On contate que les angles en A, B,C et D ne sont
plus droits et les longueurs des arcs AB et DC sont égales. Une telle
situation se produit lorsqu'on veut réaliser une flexion importante
sur une éprouvette (une poutre) très épaisse par rapport à la
longueur.
Vu la grande épaisseur, la flexion
doit entraîner des variations de longueurs considérables de DC et de AB, ce qui
entraine des contraintes de force très importantes et les différentes couches
internes entre les couches de surface AB et CD coulissent les unes sur les
autres (à l'image d'un cahier que l'on plie et dont les feuilles glissent alors
les unes sur les autres). Dans le cas des composites stratifiés, cette situation
où les couches glissent sur les autres est appelée délaminage. Les pratiquants
de l'eau vive connaissent bien ce genre de dégat sur leur bateau après une
rencontre avec un rocher. Un choc avec flexion sur une structure sandwich
entraine souvent le même résultat.
Dans les laboratoires, on utilise
souvent ce type de flexion sur des éprouvettes très épaisses, pour mesurer la
capacité d'un composite de résister au délaminage.
En conclusion, les matériaux
intéressants pour la rigidité sont ceux qui opposent une très grande résistance
à l'étirement et à la compression. Cette aptitude d'un corps à s'opposer à son
étirement est mesurée par un nombre appelé module d'élasticité.
D'une façon plus précise, la force
F qu'il faut appliquer à un échantillon cylindrique pour obtenit un
allongement dl de sa longueur est donné par F = e.s.dl / l où e
représente le module d'élasticité, s la section du cylindre et l
sa longueur (à une constance multiplicative près pour tenir compte des
unités de mesure). En écrivant F/s =e.dl/l, on contate que e est
un coefficient multiplicateur entre une pression F/s et un poucentage
d'allongement dl/l
Pour simplifier la suite de l'étude
on supposera les unités choisies de sorte à avoir s=1.
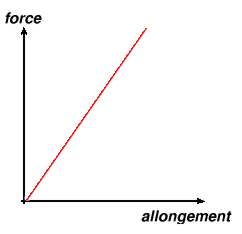
En posant x = dl/l et y= F/s on a
donc y = e.x et cette relation se représentera graphiquement par une droite
passant par l'origine de coefficient directeur e ( Rappelons que le coefficient
directeur nous indique la pente de la droite.
Dans les livres scolaires,
l'équation de la droite est souvent notée par y = ax et a est le coefficient
directeur)
Donc pour un matériau rigide cette
droite est fortement inclinée
Un corps quelconque ne peut
indéfiniment s'allonger. Quand un certain poucentage d'allongement est obtenu
sur notre cylindre de test, il se casse en deux morceaux. Comme pour le module
d'élasticité, le pourcentage d'allongement à la rupture est aussi une
caractéristique de chaque corps.
En analysant la formule précédente,
on contate que la résistance d'un matériau est donnée par le produit de son
module par son allongement à la rupture.
 Si un coprs est soumis à une
contrainte, il subit des déformations. Si celles-ci atteignent à certains
endroits des valeurs dépassant l'allongement à la rupture, le corps subit des
cassures à ces endroits.
(Cette étude faite sur les
allongements peut aussi s'appliquer à la compression et on peut définir le
module d'élasticité en compression.)
Certains corps ne se rompent pas
aussi brutalement qu'indiqué ci-dessus. Ils se cassent en quelque sorte comme un
corps pâteux.. La rupture est dite ductile par opposition à la rupture brutale
qui est dite fragile
(un matériau à rupture fragile peut
être mécaniquement très résitant)
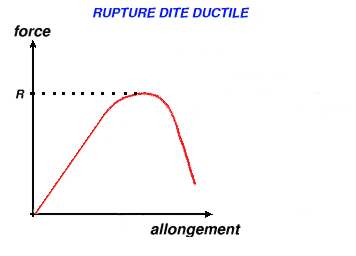
Dans ce type de rupture, on contate
qu'il existe un premier allongement en dessous duquel il n'y a aucune altération
du matériau.
Si l'étirementt se pousuit sans
atteindre l'allongement à la rupture, il se produit des déformations
irréversibles dans le corps qui ne possède plus ses qualités
d'origine.
(penser à l'étirement d'une pâte à
modeler)
Il arrive souvent qu'un corps soit
percuté par un autre. Il se pose alors le problème de l'absorbtion
d'énergie.
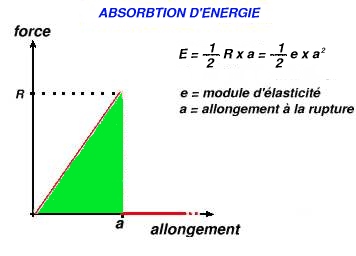
Rappelons que l'énergie mécanique
est égal au produit scalaire de la force et du déplacement.
Si la force varie pendant le
déplacement il faut utiliser la valeur moyenne de celle-ci qui est de
(½)R pour une rupture fragile.
En multipliant ce nombre par
l'allongement a on aura l'énergie maximum absorbable sans dépasser
l'allongement à la rupture.
Cette énergie correspond donc à
l'aire du triangle représentée en couleur verte
Dans le cas d'une rupture ductile
le calcul de l'énergie absorbable ne peut plus se faire aussi
simplement
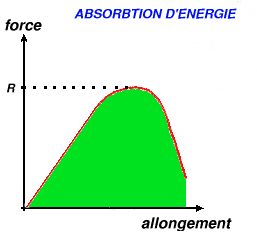
La valeur moyenne de la force n'est
plus égale à la moitié de R comme précédement.
Il faut avoir recours au calcul
intégral pour obtenir cette énergie.
Elle correspond à l'aire de la zone
représentée en couleur verte
Les paragraphes qui vont suivre
utiliseront ces notions que nous venons de voir
|